The alternating softener is more traditional in the boiler treatment industry and gives the customer a lot of wiggle room for changes in condensate return, hours of operation, water hardness, etc. If the end user is on a water management program with Nalco, Betz or the such, their service rep is more comfortable with twin alternating systems.
Options are:
- Single tank unit. Our DFT-37. One 9" Dia. x 48" high fiberglass media tank with 1.25 cu. ft. softening resin. Top mount Fleck ProFlo 5000 valve with bypass and 3/4" brass sweat in/out fitting. Metered with 7 day override. One 18" dia. x 40" high brine tank that has a brine overflow safety valve.OR
- Alternating twin unit. Our model AFT-24-1. Two (2) 8" Dia. x 44" high fiberglass media tanks with 0.75 cu. ft. softening resin in each. Control with a Fleck 9100 metered twin valve with by-pass and 3/4" brass sweat in/out fitting. One 18" dia. x 40" high brine tank that has a brine overflow safety valve.
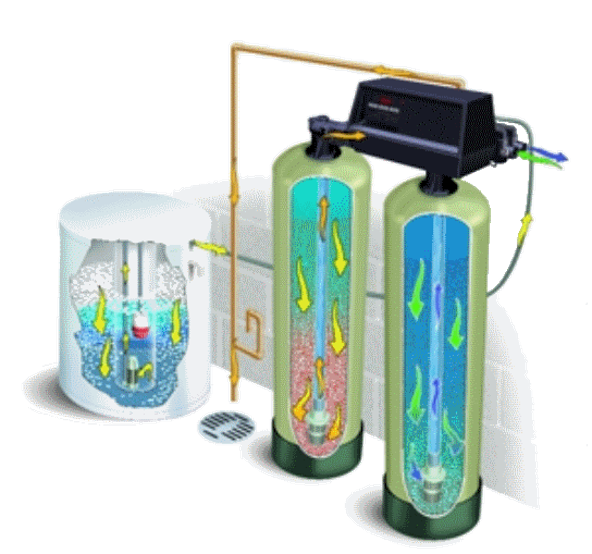
Water is considered soft if its hardness is less than 75 parts per million (ppm), moderately hard at 75 to 150 ppm, hard at 150 to 300 ppm, and very hard at 300 ppm or higher.
Water Category Water Hardness (grains/gallon): S = Soft (1 through 7.5); N = Normal (7.6 through 17); H = Hard (over 17).
Hard water contains dissolved calcium and magnesium that can stick to bathroom and kitchen fixtures. Water softeners use sodium to remove those minerals, but some softeners dump large amounts of salt into drains in the recharging process one to three times a week.
Water softening process
1. Switching minerals out
Calcium and magnesium ions in hard water are replaced with sodium ions, softening the water.
2. Recharging the unit
Plastic beads are soaked in a strong brine solution to remove the calcium and magnesium buildup and restore sodium.
*Source: Lorena I. Elebee, Los Angeles Times
I. Determine softener capacity by using method A or B below:
- A. Boiler Horsepower x 4 gallons per hour x daily hours of operation x water hardness in Grains per gallons + Daily Gallons of blow-down = Grains per Day required @ 100% Make-up. Reduce daily required capacity by the percentage of condensate return*.
- B. Pounds of Steam Per Hour Produced divided by 8.345 x Daily Hours of Operation + Daily Gallons of blow-down x Water Hardness in Grains per gallon = Grains per Day required at 100% Make-up. Reduce daily required capacity by the percentage of condensate return*.
II. Determine Flow Rate of softener using method C or D below:
- C. Boiler Horsepower x 4 gallons per hour + estimated rate of blow-down in G.P.M. = G.P.M. required.
- D. Pounds of Steam per Hours divided by 8.345 divided by 60 minutes + estimated rate of blow-down in G.P.M. = G.P.M. required.
III. Select a Softener that will produce the required capacity & flow rate.
In layman’s terms:
Boiler Horsepower x 4 gallons per hour = Amount of Water required per hour. Example: A 25 hp boiler x 4 (GPH) = 100 gallons per hour x 8 hours of operation = 800 gallons per day. Normal exchange rate @ 6# of salt per cubic foot High Capacity Resin is 24,000 grains exchange. Divide 24,000 grains by the raw hardness of make-up water. If the water has 15 grains of hardness, (24,000 ÷ 15 grains = 1600 gallons per cubic foot of soft water per regeneration) deduct the percentage of return from total required per hour (100 gallons x 50% condensate return* = 50 gallons per hour) For blow-down GPM simply add 5% to required make up per hour.
*Even if all heat using equipment has steam traps and the condensate return appears to be 100%, never estimate over 85% return.